Top-Down Timing Design
by Brian Hoyer and Donna Mitchell
Appeared in Integrated System Design magazine, July 1997
Download article in Acrobat format
What isTop-Down Timing Design?
Generally when a design is started, a designer is given high level timing requirements that must be
met by his design. Examples of high-level timing requirements include computational throughput (e.g.
millions of instructions per second), data transmission rates (e.g. megabytes per second), and response
latencies to requests from external systems. A designer takes these times and converts them into cycle
times (for example, 10 MIPS = 100ns per instruction). These cycle times serve as "timing budgets" for
the designer that he must work within during the design of his system. As the design is broken down
into smaller and smaller subsystems, the cycle times are subdivided and assigned to each subsystem.
The process of moving through each successive level of timing is top-down timing design.
How does Top-Down Timing Design differ from Back-End Timing Analysis?
The key feature of a top-down timing design methodology is an upfront analysis of system timing (usually
using timing diagrams) right at the beginning of the design cycle where errors can be quickly corrected.
Back-end timing analyzers such as digital simulators and static timing analyzers require the designer
to have already committed to a specific circuit implementation (usually specified as a schematic or
HDL netlist with associated simulations models). This requirement for a nearly completed design prior
to beginning timing analysis means that any timing errors discovered during a back-end analysis may
result in a significant redesign effort. In addition, when timing or logic errors are found at this
stage, any circuit changes must be reflected in many different places: the schematic, model descriptions,
test bench stimulus for the simulator or timing analyzer, and documentation accompanying the design.
Top-down timing design helps the designer discover timing errors earlier in the design cycle, resulting
in fewer changes and faster product development.
Back-end timing analyzers are most useful as design sign-off validators rather than as design aids.
It is difficult to use a back-end timing analyzer to maximize design speed because most of the design
decisions have been made by the time a back-end timing analysis begins. Examination of significantly
different design choices is not possible because each design alternative requires too much front-end
design time before its performance can be analyzed. Front-end timing analyzers such as WaveFormer Pro
by SynaptiCAD Inc. (see Figure 1), excel at timing optimization because comparatively little design
information needs to be entered in order to analyze system performance.
Front end timing analyzers don't invalidate the use of back-end timing analyzers. While front end timing
analyzers are quicker and require less design entry, back-end timing analyzers benefit from having complete
design information and generally perform a more exhaustive, brute force analysis of a design's performance
that can detect errors that a designer may have neglected to check for during a front-end timing analysis.
In fact, one of the biggest challenges of using a back-end timing analyzer is sifting through the data
generated by the analysis to discover real timing errors. Nonetheless, the additional security provided
by a back-end timing analysis prior to design sign-off argues for the combined use of a front and back-end
timing analyzer when using a top-down design approach.
Benefits of timing diagram analysis
Designer's have traditionally used hand-drawn timing diagrams to perform their initial timing analysis.
Timing diagrams offer the advantage of being able to see the effects of timing constraints on a system's
signals. With a timing diagram, the cause-effect relationships between signal transitions are shown
by timing parameters such as delays, setups, and holds, providing a designer with more insight into
the operation of a system. This is particularly helpful because timing errors are found early in the
design cycle. Also critical paths that cause errors can be analyzed visually by following delay chains
back through the diagram. Each delay in a critical path suggests a point at which a circuit change could
alleviate a timing error or increase system performance.
Figure 1. Timing diagram used for top down timing design. The screeen capture of WaveFormer Pro shows
margin calculations and delay parameters.
Timing diagram analysis also gives you the advantage of being able to account for min/max delay tolerances
at the same time. This is critical for asynchronous designs such as bus transaction protocols because
most simulators can only simulate at the extreme timing end points, but not over the entire operational
range of the design.
Many designs are never given a thorough timing diagram analysis, despite the benefits, because of the
amount of time required to perform such an analysis manually. Drawing timing diagrams by hand is a difficult
and error prone task and the resulting diagrams are generally messy and hard to understand and analyze.
The messiness is compounded when timing errors are discovered and fixed causing the hand drawn timing
diagrams to be erased and redrawn. In addition, the timing analysis of manually generated timing diagrams
is usually overly pessimistic because it is difficult to find and remove common delays from setup and
hold calculations.
Timing diagram editors such as WaveFormer eliminate the need to manually generate timing diagrams, making
it easy to create and change timing diagrams and reducing the chance for error in timing calculations.
Timing diagrams can be created with a combination of point-and-click drawing, Boolean and temporal equations,
and auto-generated clocks and busses. Designers can analyze system performance using just the timing
parameter information available in data books without the need for schematic netlists and complex simulation
models. Timing calculations are performed interactively, so it is easy to quickly assess the impact
of a change in a timing parameter by updating the parameter's value or switching to a different part
library.
Timing diagram editors can provide several types of timing and logic analysis:
- Automatic calculation of critical paths and constraint checking (setup and hold margins)
- Common delay removal
- Delay correlation calculations
- Combinatorial logic analysis using Boolean equations
- Temporal equations for DSP analysis
- Reuse of timing during simulation
Calculation of Critical Paths and Constraint Checking
Timing calculations in a timing diagram analyzer are performed using true min/max timing, and calculations
are automatically adjusted to account for subtle timing effects such as reconvergent fanout. With timing
diagram editor output, it is easier to see timing relationships between signal transitions than with
a simulator, because the timing parameters (propagation delays, setup times, and hold times) graphically
specify cause/effect relationships between signal transitions and timing constraints that must be met
by the system. This is one reason engineers still draw timing diagrams by hand even when they have access
to powerful simulators. Timing diagram editors also allow designers to verify min-max timing simultaneously
so that the overall impact of IC timing tolerances on a system.s performance can be properly assessed.
Reconvergent Fanout
Margin calculations in some circuits can be overly pessimistic if all the uncertainty times in a timing
path are included in the calculations. For instance, if two signal transitions B1 and B2 are caused
by the same transition A (see Figure 2), then margin calculations between B1 and B2 should not include
the uncertainty of transition A, because no matter when A transitions it will occur at the same time
for both B1 and B2. When this happens the circuit is said to have reconvergent fanout, because this
typically occurs when two signals diverge (fanout) from a common source and reconverge at the inputs
of a gate. The adjustment of timing calculations to account for reconvergent fanout is referred to as
common delay removal, because the uncertainty created by delays common to both timing paths is removed.
The ability to recognize and remove the pessimistic effects of reconvergent fanout is especially important
for circuits with demanding timing requirements. Performing common delay removal on manually drawn timing
diagrams is tedious and error prone, but ignoring this effect can lead to sub-optimal designs.
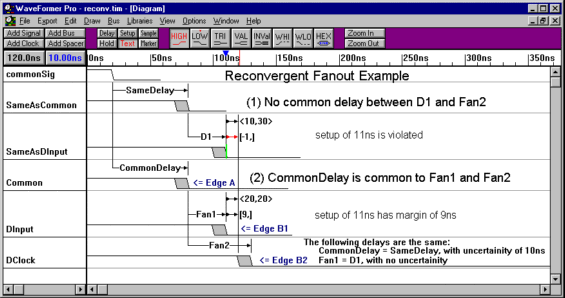
Figure 2. Reconvergent fanout example. Reconvergent fanout adjustment removes common delays from calculation
margin and distance values.
Delay Correlation
Another effect that is rarely accounted for in digital designs that can lead to overly pessimistic margin
calculations is delay correlation. Delay correlation allows the designer to specify that the degree
of variation in gate delays on a single chip is smaller than the variation of gate delays across multiple
chips. This lower variation in on-chip delays makes it possible for designs to meet setup and hold time
requirements that could not be met using just the min/max delay values.
Delay correlation is expressed as a percentage value. By default, delays in WaveFormer Pro are considered
uncorrelated (delay correlation = 0%). 100% delay correlation between a group of gates would mean that
all the gates are guaranteed to have exactly the same propagation delay time. Note that this delay time
could be anywhere between the min and max time of the delay parameter, but whatever the value it would
be the same of all the gates. For example, two gates with a min/max delay = 5-15 ns and a correlation
of 90% could have delay values anywhere in the range between 5 and 15 nanoseconds, but the delays of
the gates are guaranteed to be within 1 nanosecond ( (15ns - 5ns)*90% = 1ns) of each other.
Process and temperature variations across ICs account for the increased variation in across-chip gate
delays. IC manufacturers do not generally publish delay correlation values for most standard TTL and
CMOS parts, but they do publish delay correlation values for clock buffer ICs (correlation between clock
delays is more important than absolute delay for clock trees as uncorrelated delays increase clock skew).
Clock buffer delay correlation is usually specified indirectly as a min/max delay and an on-chip delay
variation often called skew (e.g clock buffer with delay = 5-10 ns and on-chip skew = 1ns has a delay
correlation of 80% ( 100% - 1ns / (10ns - 5ns) = 80%).
Designers using ASICs and FPGAs will benefit the most from taking advantage of delay correlation in
their designs, since most of the delays in these designs are correlated. If your gate array or FPGA
manufacturer doesn.t publish this information in their data books, you should ask your manufacturer
directly as they probably have the information available internally. The primary reason delay correlation
information hasn.t been published much in the past has been the lack of EDA tools that can take advantage
of it.
Correlation factors in WaveFormer Pro are specified by first creating a correlation group name and assigning
it a correlation percentage. Next all the correlated delays (e.g. all the delays on the chip) are added
to the correlation group. For gate array designers, WaveFormer Pro supports a default correlation group
which applies to all delays in a design. After delay correlations are specified WaveFormer Pro automatically
adjusts all timing margins in a design.
Combinatorial Logic Analysis
Early in the top-down design cycle, after the original timing interface has been analyzed, different
parts of the circuit will start to take shape. WaveFormer Pro helps you in this phase by supporting
interactive Boolean simulation (see Figure 3). Designers can enter Boolean equations that describe their
design and immediately assess the impact of modifying logic, state, and timing information without having
to change a schematic or create simulation models. The Boolean simulator includes support for propagation
and interconnect delays allowing any combinatorial logic to be modeled. Below is an example of a Boolean
equation that models an AND gate with an input delay of 20ns on one input and 10ns on the other input:
SIG3 = (SIG0 delay 20ns) and (SIG1 delay 10ns)
Figure 3. Interactive Boolean simulator example. Interactive Boolean simulation aids in top-down timing
analysis.
Temporal equations for describing DSP waveforms
Many waveforms are difficult to draw and work with because of the precise edge placement necessary to
convey circuit information. For instance, a waveform that alternates between a frequency of 25MHz and
50Mhz for 10 cycles would be very tedious to attempt to draw by hand. These types of waveforms can be
described in WaveFormer Pro using temporal equations. The waveform described above could be generated
using the following temporal equation:
CK25_50 ( (20=H 20=L)*20 (10=H 10=L)*20 )*10
Reuse timing diagrams during Simulation
WaveFormer Pro can be used as a stand-alone design verification tool or in conjunction with a digital
simulator. All simulators need input stimulus to perform a simulation. With WaveFormer Pro, waveform
data can be saved to different simulator formats for driving simulations (e.g. VHDL, Verilog, Spice,
Mentor's Quick Sim II, Viewlogic, OrCAD, Model Tech V-System, and Accolade PeakVHDL formats). In addition,
WaveFormer Pro supports the import of waveforms from other tools, so it can serve as a translator between
different waveform formats. WaveFormer Pro uses a scripting language based on Perl (Practical Extraction
and Report Language) to import and export waveform stimulus. The use of a scripting language means users
can modify the output of existing translation scripts and even create their own scripts to support waveform
formats used by custom test equipment and internally developed software.
Summary
Top down design is the process of starting from a high-level specification of a system and moving down
through successive level of detail until a design is completed. Top down timing analysis is a natural
design paradigm which fits well with interface specifications and component information taken from data
books. Top-down timing analysis is difficult and error prone when performed using manually generated
timing diagrams, but timing diagram editors such as SynaptiCAD's WaveFormer Pro make timing diagram
analysis a rapid and relatively painless process. Timing diagram editors allows the generation of detailed
timing diagrams that are vastly easier to create and maintain than those that can be generated using
conventional drawing packages. Rapid design entry and rapid feedback on system functionality makes timing
diagram software ideal tool for the iterative process of designing digital circuits and examining design
tradeoffs in a "what-if" fashion. Some useful analysis features of timing diagram editors can include:
Boolean equation simulation, critical path analysis, setup/hold margin calculation, removal of common
delays from margin calculations (reconvergent fanout analysis), and timing adjustment for delay correlation.
Top-down timing analysis using a timing diagram editor provides benefits throughout the design process.
As a system specification and analysis tool, a timing diagram editor is particularly useful for pre-schematic
analysis before simulation is possible. During the design phase a timing diagram editor can serve in
a dual role as timing analyzer and test bench generator for simulations. During the documentation phase
of a design, the timing diagrams generated during the top-down design process serve as a useful adjunct
to schematics and other design documentation.
Bryan Hoyer is president of Boulder Creek Engineering, Saratoga CA, the makers of the Pod-A-Lyzer.
He has over 20 years of experience designing digital and analog systems.
Donna Mitchell is vice president of marketing for SynaptiCAD Inc.
Technical Paper Home Page
|